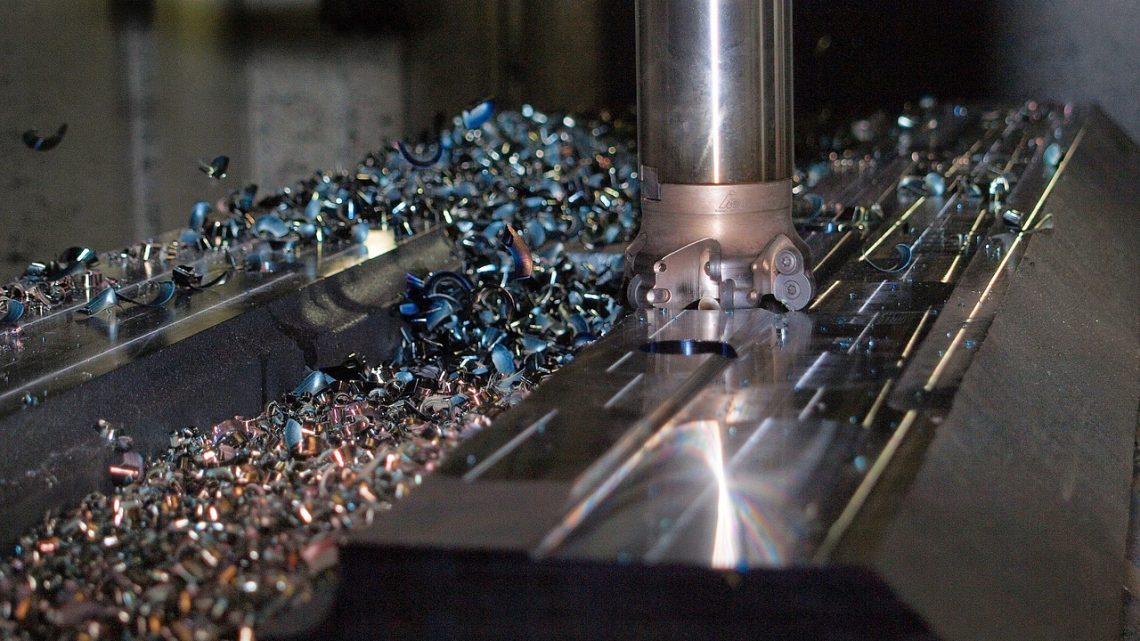
Programowanie i optymalizacja parametrów toczenia CNC
12 maja 2025W dzisiejszych czasach przemysł produkcyjny coraz bardziej opiera się na zaawansowanych technologiach obróbki skrawaniem, w tym na toczeniu CNC (Computer Numerical Control). Ta metoda pozwala na uzyskanie wysokiej precyzji i powtarzalności w obróbce różnych materiałów, od metali po tworzywa sztuczne. Kluczem do osiągnięcia optymalnych rezultatów jest odpowiednie programowanie maszyn CNC oraz staranna optymalizacja parametrów toczenia, co w efekcie zapewnia toczenie precyzyjne i ekonomiczne. W artykule omówimy najważniejsze aspekty związane z programowaniem i doborem parametrów w procesie toczenia, z naciskiem na znaczenie precyzji i efektywności produkcji.
Programowanie CNC w kontekście toczenia precyzyjnego
Podstawą skutecznego toczenia CNC jest poprawne przygotowanie programu obróbki, który dokładnie odzwierciedli zamierzony kształt, wymiar i powierzchnię wyrobu. Programowanie CNC opiera się na językach takich jak G-code, które precyzyjnie określają ruchy narzędzia, prędkości, posuwy oraz inne parametry. W przypadku toczenia precyzyjnego kluczowe jest odpowiednie zaprogramowanie każdego z tych elementów, aby minimalizować odchylenia od wymaganego kształtu i wymiarów. Warto zwrócić uwagę na konieczność uwzględnienia współczynników rozszerzalności materiału, elastyczności narzędzia czy ewentualnych drgań, które mogą wpływać na końcową jakość obróbki. Skuteczne programowanie obejmuje także wykorzystanie funkcji specjalnych, takich jak interpolacja kołowa czy korekta geometrii narzędzia, które pozwalają na jeszcze dokładniejsze odwzorowanie kształtu. Zaawansowane systemy CAD/CAM umożliwiają generowanie programów CNC z poziomu modeli 3D, co ułatwia tworzenie dokładnych trajektorii narzędzia i zmniejsza ryzyko błędów.
Optymalizacja parametrów toczenia dla toczenia precyzyjne
Dobór odpowiednich parametrów toczenia jest kluczowy dla osiągnięcia toczenia precyzyjnego i minimalizacji odpadów. Wśród najważniejszych parametrów znajdują się prędkość obrotowa (n), posuw (f), głębokość skrawania (ap) oraz prędkość posuwu narzędzia. Optymalne ustawienia tych wartości zależą od rodzaju materiału, geometrii narzędzia oraz wymagań dotyczących jakości wykończenia. Na przykład, w przypadku obróbki twardych metali, takich jak stal hartowana, konieczne jest zastosowanie mniejszych posuwów i niższych prędkości, co pozwala na precyzyjne cięcie bez przegrzewania narzędzia i materiału. Z kolei podczas toczenia miękkich materiałów można zwiększyć prędkości i posuwy, co przyspiesza cały proces. Kluczem do skutecznej optymalizacji jest stosowanie metod statystycznych i symulacji, które pozwalają na dobór parametrów w sposób jak najbardziej zbliżony do rzeczywistych warunków obróbki. Regularne testy i modyfikacje parametrów na podstawie wyników końcowych pozwalają na ciągłe doskonalenie procesu i uzyskiwanie toczenia precyzyjne na najwyższym poziomie.
Techniki wspomagające toczenie precyzyjne
W celu zapewnienia toczenia precyzyjne coraz częściej stosuje się różnorodne techniki wspomagające. Należą do nich m.in. monitorowanie stanu narzędzia, które pozwala na wczesne wykrywanie zużycia i wymianę narzędzia w optymalnym momencie. Systemy czujników i automatyczne korekty trajektorii narzędzia umożliwiają eliminację odchyłek i minimalizację błędów podczas produkcji. Kolejną istotną techniką jest stosowanie specjalnych narzędzi z powłokami antykorozyjnymi i zwiększającymi trwałość, co przyczynia się do stabilizacji parametrów toczenia i poprawy jakości wykończenia. Współczesne systemy CNC wyposażone są również w funkcje automatycznego dostosowania parametrów w trakcie obróbki, co pozwala na dynamiczne reagowanie na zmieniające się warunki pracy. Dodatkowo, programowanie z wykorzystaniem symulacji komputerowych umożliwia wczesne wykrycie potencjalnych problemów i optymalizację trajektorii narzędzia, co jest szczególnie ważne w przypadku toczenia precyzyjne, gdzie nawet najmniejsze odchylenia mogą mieć znaczący wpływ na końcową jakość produktu.
Wyzwania i przyszłość toczenia CNC
Zastosowanie technologii toczenia CNC niesie ze sobą szereg wyzwań związanych z koniecznością ciągłego doskonalenia parametrów i programów. Współczesne maszyny coraz bardziej integrują funkcje automatycznego monitorowania i korekty, jednak wciąż wymaga się od operatorów i inżynierów dużej wiedzy i doświadczenia, aby w pełni wykorzystać potencjał tych rozwiązań. Rosnące wymagania dotyczące jakości i precyzji produkcji powodują, że coraz większy nacisk kładzie się na automatyzację i inteligentne systemy optymalizacji parametrów toczenia. W przyszłości można spodziewać się rozwoju technologii sztucznej inteligencji, które będą analizować dane z procesu w czasie rzeczywistym i automatycznie dostosowywać parametry, minimalizując ryzyko błędów i zwiększając wydajność. Ponadto, postęp w dziedzinie materiałów narzędziowych i powłok zwiększy trwałość narzędzi, co pozwoli na dalsze zwiększanie precyzji toczenia przy jednoczesnym obniżeniu kosztów. Zintegrowane systemy CAD/CAM oraz zaawansowane algorytmy optymalizacji będą odgrywały kluczową rolę w realizacji jeszcze bardziej precyzyjnych i wydajnych procesów toczenia CNC, zapewniając toczenie precyzyjne na najwyższym poziomie i spełniając rosnące oczekiwania przemysłu.